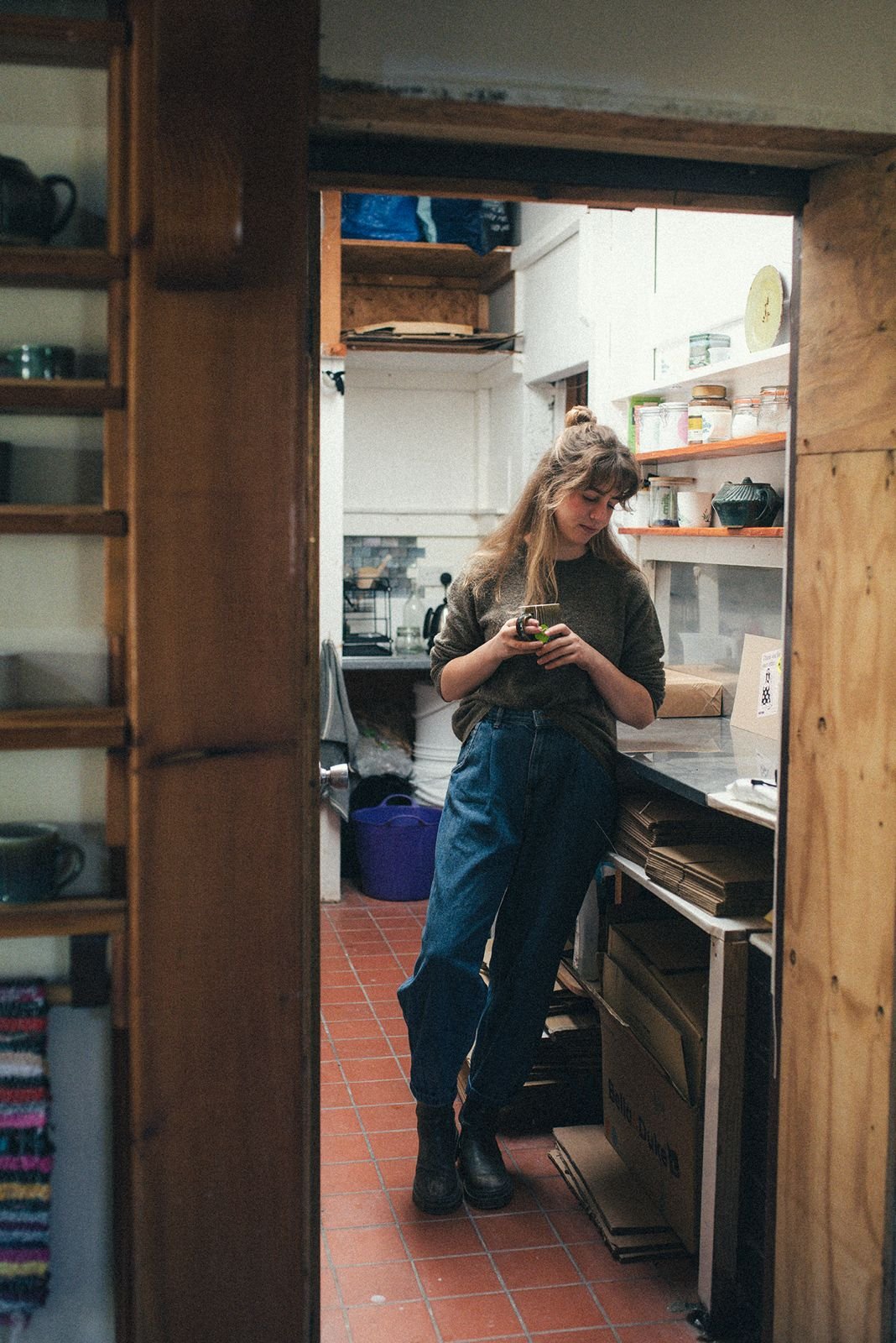
I’m Anna MacDonald, a small-batch production potter from the Isle of Tiree. I make wheel-thrown and hand-built tableware, inspired by Scotland’s West Coast and the Hebrides. My focus as a potter is on pieces that are comforting to touch or to hold; durable pots for everyday use with the beauty of a West Coast shoreline reflected in their design.
I named the pottery Eòrna, the Scottish Gaelic for barley - Tiree is known poetically as Tìr Ìosal an Eòrna or ‘the low lying land of the barley.’ I grew up firmly rooted in the Gaelic culture of the island, and it’s as much a part of me as it is my practise.
I’ve worked for various brilliant tableware potters across Scotland for the last decade, from Helen and Jean Oldfield at Tyrii Pottery making slip decorated earthenware to Jen Smith at Wild Gorse making contemporary yet traditional stoneware. I didn’t study ceramics, I’ve learnt everything I know on the job or during apprenticeships - I studied music and was a traditional musician for years but made it work alongside pottery before choosing to focus on tableware full-time in 2020.
More recently I’ve moved to Kilchoan, Ardnamurchan to set up my own studio, and my collection has expanded to incorporate aspects of the beautiful landscape here. Ardnamurchan has strong connections with the Inner Hebrides, culturally and geographically, and I’m loving building a life here with my partner as I develop new work.
I’m now entering my second year in this studio, selling pieces online and wholesale with various stockists, and working towards opening a small shop at the front of the studio from the end of May (2025).
If you’d like to see more of what I do day to day, you can follow my instagram page @eornapottery for any updates, or sign up to my mailing list on the home page.
About me.
I make my pots in small batches, usually working on between fifteen and forty at a time. The slab-building, hand-building, wheel-throwing and glazing that goes into the creation of a piece of Eòrna pottery show the marks of handmade ceramics - each piece is entirely unique.
When people think of pottery, they often imagine someone throwing on the wheel, but in reality that’s often only the first part of the process. For example, here are the rough steps I go through to make one of my carved coffee cups:
I first prepare some clay by wedging it together for a smoother consistency and to get rid of any trapped air. I then weigh out my clay so that each mug is made with the same amount, and then I get to throwing, measuring as I go with my hands and with a throwing gauge for consistent pieces that fit their purpose.
There is a lot of water in clay, and more water is added during the throwing process to avoid friction, so these mug ‘bodies’ are placed on a ware board together to dry until about fifty percent of the water has gone. This can take days in the Scottish winter when the moisture content in the air is generally higher.
Once the bodies are at a ‘leather hard’ stage, I put them on the wheel again to trim off any excess clay and refine the walls and the base. I can then attach a handle by ‘pulling’ one off the pot using a small stub of clay and more water. I can also carefully carve into the walls, and add my maker’s mark on the base.
The mugs can then be left to dry slowly until they are ‘bone dry’. Only then can they go in the kiln - if excess moisture is left in a pot when fired it can cause the pot to explode. I bisque fire my pots to 1000 degrees celsius in an electric kiln, and once they’re cooled and unloaded, I can glaze.
I apply wax resist to the base of any bisque fired pots to prevent any glaze absorbing there, and then pour glaze onto my pots or dip them into buckets of glaze I’ve pre-mixed. I then clean off the bases and leave them to dry again for twelve hours or so.
Finally, I reload the kiln for a glaze firing, reaching temperatures of around 1250 degrees. The glaze creates a layer of glass over the pot, and what comes out of the kiln is (with any luck and a whole lot of skill) a fully vitrified carved coffee cup!